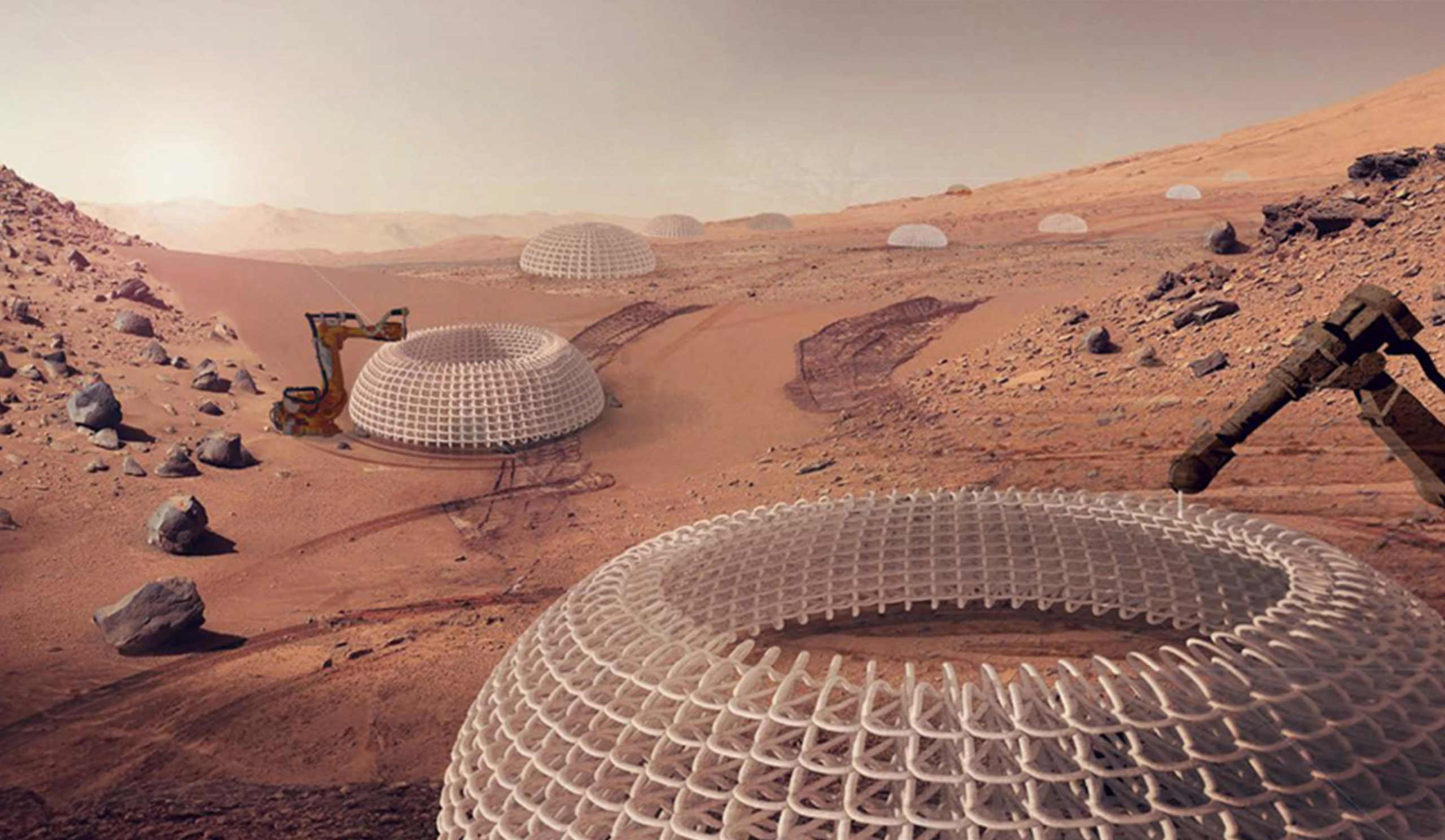
Digital Fabrication + Spatial Printing
Over the last two decades, digital fabrication tools such as laser cutting, 3D printing, and CNC milling machines have become broadly accessible to designers. The design and manufacturing workflow allows us to build a complex, tangible model directly from digital data. However, due to limitations of size and workable materials, it has not been widely used throughout the construction industry.
As an advanced digital fabrication tool, robotic fabrication has been explored by many researchers who believe it could be a new paradigm in the construction industry. The ability to fabricate complex geometries by using 6-axis movement and mobility to overcome the size limitation has made robotic fabrication even more compelling.
From this perspective, three researchers at Harvard Graduate School of Design explored a spatial printing methodology. Unlike conventional additive manufacturing processes, the spatial printing methodology — Spatial Print Trajectory (SPT) — takes advantage of the viscous material properties of clay by integrating material-specific properties into the 3D printing process and controlling print speeds accordingly.
A series of maneuvers that simulate anchoring and dragging actions allowed for the creation of complex, self-supporting clay lattices. Further research integrated an automated recalibration process to predict material uncertainties that occur during the printing process. Augmentation of the recalibration process spawned the Responsive Spatial Print Trajectory (RSPT), which is a closed-loop printing framework that adjusts the position of imminent digital tool path commands based on measured values via a laser sensor. Accordingly, the inevitable discrepancies between the digital tool path and the printed geometry were able to compensate.
The research further explored the entire process of improving observed limitations and applying the aforementioned methodologies to large-scale construction. The results from rigorous material tests allowed the authors to understand viscous materials in depth and overcome limitations of 3D clay printing. First, three different clay bodies were tested. Distortion was minimalized through a fiber mix that binds clay and enhances structural integrity within the drying process. Additionally, an improved recalibration process expedited a sensing process with increased accuracy in measurement. Lastly, its application to a large-scale construction was demonstrated by building a 1.2m x 1.2m x 2m pavilion within five days. Through the process, researchers successfully accomplished proving the compatibility of developed methods and the possibility for its utilization in large-scale construction with an ability to control the process remotely.
From understanding material properties to improving printing process with recalibration, the entire methodology by the researchers opens up opportunities for utilizing viscous materials for in-situ printing.
Reference
-
ALOTHMAN, S, H. IM, F. JUNG, AND M. BECHTHOLD. 2018. “SPATIAL PRINT TRAJECTORY: CONTROLLING MATERIAL BEHAVIOR WITH PRINT SPEED, FEED RATE, AND COMPLEX PRINT PATH.” IN ROBOTIC FABRICATION IN ARCHITECTURE, ART AND DESIGN, EDITED BY J. WILLMAN, P. BLOCK, M. HUTTER, K. BYRNE, AND T. SCHORK. CHAM, SWITZERLAND: SPRINGER.
- H. IM, ALOTHMAN, S., GARCÍA DEL CASTILLO Y LÓPEZ, H. 2018 “RESPONSIVE SPATIAL PRINT: CLAY 3D PRINTING OF SPATIAL LATTICES USING REAL-TIME MODEL RECALIBRATION”, AACADIA CONFERENCE.